IHTS Case Studies
For over two decades, IHTS has optimized heat treating for our part making customers. Our consultants integrate the optimal heating and quenching techniques for the different alloy materials and the intended end users.
Here are some specific examples how IHTS Consultants provides more added value to heat treated and forged parts.
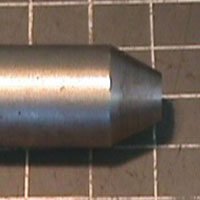
Lean, Integrated Heat Treating for S-5 Tool Steel Punches
The expected failure mode for an S-5 tool steel cold working punch is chipping of the cutting edge after making a certain number of holes. After oil quenching the punch is 60-61 HRC and does not have much ductility. However, after an intensive water quenching the same design punch made of the same S-5 alloy steel tempered to the same hardness will punch 2 to 9 times more holes.
Learn more.Shorten or Eliminate Case Carburizing Cycles for “Case Hardened and Core Toughened” Steel Parts
Reduce or eliminate long-batch carburizing cycles and still provide higher levels of beneficial residual compressive surface stresses for longer cyclic fatigue life. This is because the surface compression holds the hard grains together and this compressive force must be overcome before the part will begin to bend and then fatigue.
Learn more.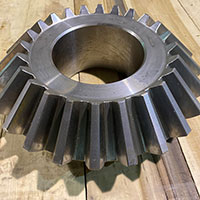
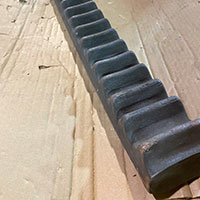
Lean, Integrated Heat Treating for Field Repairability
To have “Field Repairability” in a part design and still have the needed strength in the part, the material alloy selected and the heat treating process must be integrated. The designer must select an alloy of steel that is weldable without pre- and post-heating in the field to prevent cracking, and yet still deliver the needed mechanical properties. For example,
Learn more.Lean, Integrated Heat Treating for Ductile Iron Castings
For many years, ductile iron castings have been given improved mechanical properties with austemper heat treat quenching processes in hot salt. Austempered Ductile Iron (ADI) was pioneered by Applied Process in close collaboration with the ductile iron foundries. Due to their superior mechanical properties, high ductility, low
Learn more.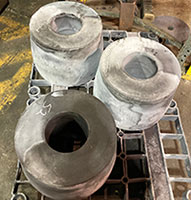
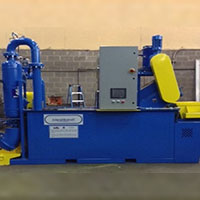
Lean, Integrated Heat Treating for Direct from the Forge Intensive Quenching
Lean integrated heat treating solutions cannot be fully implemented without the development of the proper heat treating equipment. With Direct from the Forge Intensive Quenching (DFIQ) equipment on the forging shop floor, the forger is also the part heat treater; the forger becomes a “captive heat treater” adding more value to the forger’s link
Learn more.